- Registriert
- 12.12.2020
- Beiträge
- 255
Leider stoße ich beim Testen gerade auf Probleme: Die Trapezspindel wird bei zu großer Kraft aus dem Getriebe gezogen:
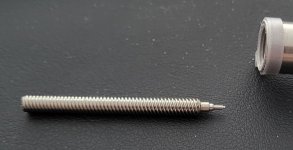
Das war die ursprüngliche Ursache:
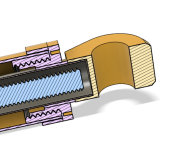
Beim Anschlag hinten kann die Gewindespindel ca. 2mm weit rausgezogen werden, bevor sie an einen Anschlag kommt.
Zunächst dachte ich: kein Problem. Dann sorge ich für einen Anschlag im Kolbenauge. Aber das ist nicht weit genug gedacht. Auch, wenn der Bagger zu viel Kraft beim Baggern aufwendet kann das (theoretisch) passieren. Bei der Recherche bin ich auf einen Beitrag in einem Nachbarforum gestoßen, wo genau dieses Problem beschrieben wird: "Die Motoren haben 1mm steigung. sind aber leider nicht auf den Dauerbetrieb unter zug auf der spindel ausgelegt. hab Sie bei mir in meinen 1:32 Baggern im Arm und muss sie regelmäßig tauschen".
Ich weiß noch nicht, wie ich damit umgehe. Gerade versuche ich, die Spindel mit Loctite 648 einzukleben. Das ist nicht leicht, da die Gefahr besteht auch beweglichen Teile zu verkleben.
Am Ende müssen es vielleicht doch Endschalter sein. In den Zylindern ist praktisch kein Platz. Es ginge nur, indem man mit Hall Sensor und Ring Magnet den Winkel misst. Aber das verlangt an jedem Drehpunkt noch mal drei Adern für den Hall Sensor.
Ich habe auch gehört, dass man mit "normalen" N20 Motoren und einer Kupplung Arbeitet. Aber das würde den Verfahrweg empfindlich kürzen.
@mabuse61 Du hattest das bei Deinem Fuchs, wenn ich mich recht erinnere, mit Endschaltern umgesetzt. Richtig?
Das ist ein ziemlicher Rückschlag und ich muss erst einmal darüber nachdenken. Das Problem ist: die Getriebe Motore haben so viel Kraft, das sie sich selbst zerlegen können.
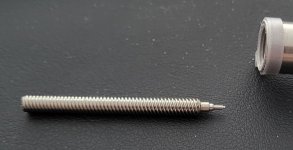
Das war die ursprüngliche Ursache:
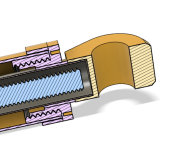
Beim Anschlag hinten kann die Gewindespindel ca. 2mm weit rausgezogen werden, bevor sie an einen Anschlag kommt.
Zunächst dachte ich: kein Problem. Dann sorge ich für einen Anschlag im Kolbenauge. Aber das ist nicht weit genug gedacht. Auch, wenn der Bagger zu viel Kraft beim Baggern aufwendet kann das (theoretisch) passieren. Bei der Recherche bin ich auf einen Beitrag in einem Nachbarforum gestoßen, wo genau dieses Problem beschrieben wird: "Die Motoren haben 1mm steigung. sind aber leider nicht auf den Dauerbetrieb unter zug auf der spindel ausgelegt. hab Sie bei mir in meinen 1:32 Baggern im Arm und muss sie regelmäßig tauschen".
Ich weiß noch nicht, wie ich damit umgehe. Gerade versuche ich, die Spindel mit Loctite 648 einzukleben. Das ist nicht leicht, da die Gefahr besteht auch beweglichen Teile zu verkleben.
Am Ende müssen es vielleicht doch Endschalter sein. In den Zylindern ist praktisch kein Platz. Es ginge nur, indem man mit Hall Sensor und Ring Magnet den Winkel misst. Aber das verlangt an jedem Drehpunkt noch mal drei Adern für den Hall Sensor.
Ich habe auch gehört, dass man mit "normalen" N20 Motoren und einer Kupplung Arbeitet. Aber das würde den Verfahrweg empfindlich kürzen.
@mabuse61 Du hattest das bei Deinem Fuchs, wenn ich mich recht erinnere, mit Endschaltern umgesetzt. Richtig?
Das ist ein ziemlicher Rückschlag und ich muss erst einmal darüber nachdenken. Das Problem ist: die Getriebe Motore haben so viel Kraft, das sie sich selbst zerlegen können.