Clodda
New member
- Registriert
- 10.12.2012
- Beiträge
- 427
Liebe Modellbaufreunde,
an dieser Stelle möchte ich versuchen ein paar grundsätzliche Fragen zum Thema der hydraulischen Anlagen zu klären und habe dazu mit der Erlaubnis von Winni (Admin) diesen FAQ-Bereich gegründet. Ich möchte dabei auch das Thema der Berechnungsgrundlagen erläutern. Ich werde die grundsätzlichen Funktionen von hydraulischen Anlagen erklären und auf die Komponenten eingehen. Ein paar Formeln sind zudem ebenfalls sinnvoll. Ich werde dabei teilweise in kleinen Schritten vorgehen, sodass es alle gut verstehen können. Viele von euch werden das meiste schon kennen, ich möchte insbesondere Einsteigern die Möglichkeit geben grundsätzliche Dinge zu verstehen.
Hintergrund: Ich selbst bin junger Maschinenbauingenieur und kenne mich in dem Bereich der Hydraulischen Systeme aus. Häufig liest man in Foren viel „Unfug“ und falsche Dinge. Grundsätzlich möchte ich das Thema allen etwas besser zugänglich machen. Ich hoffe es gefällt euch! Lob / Kritik sind gerne willkommen! Der Aufbau dieses FAQ-Bereichs wird etwas dauern.
1. Einleitung:
Hydraulische Anlagen erfreuen sich im Bereich des Modellbaus einer wachsenden Beliebtheit. Diese Anlagen bringen sehr viel Kraft auf und sind dabei meistens kompakter, kraftvoller und dynamischer als z.B. Spindelantriebe. Gleichzeitig aber auch komplexer und deutlich teurer.
Fangen wir an. Die wichtigste Formel im Bereich der Hydraulik ist folgende:
P=F/A (Druck ist gleich Kraft pro Fläche)
Ein Druck entsteht somit immer durch die Einwirkung einer Kraft auf eine Fläche.
P = Druck [Pascal oder bar]
F = Kraft [Newton]
A = Fläche [Quadratmeter]
Eine Kraft ergibt sich wie folgt
F=m*g (Kraft ist gleich Masse mal Beschleunigung)
F = Kraft [Newton]
m = Masse [Kilogramm]
g = Erdbeschleunigung (Konstante 9,81 m/s^2 )
2. Hydraulikzylinder
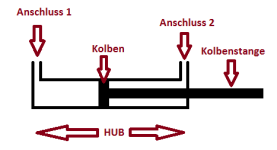
Die Abbildung zeigt einen doppelt wirkenden Hydraulikzylinder. Dieser kann in beide Richtungen (nach links und nach rechts) wirken. Es gibt auch Zylinder mit nur einem Anschluss z.B. bei einer Hebebühne für Pkw. Zum Anheben muss ich einen Druck aufbringen. Für das Absenken nehme ich den Druck wieder weg, den Rest erledigt die Schwerkraft.
In unserem Beispiel sind die wichtigsten geometrischen Daten der Kolbendurchmesser, der Kolbenstangendurchmesser und der Hub. Der Hub hat grundsätzlich nichts mit dem Druck zutun, aber dazu ein Beispiel:
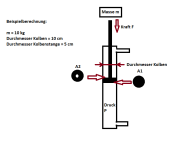
Nehmen wir an ihr wollt eine Masse von 10 kg anheben. Die Masse wirkt entgegen der Erdanziehungskraft. Es entsteht eine Kraft von:

Ihr müsst nun also eine Kraft von mehr als 98,1 aufbringen. Die Kraft wirkt über die Kolbenstange des Zylinders auf die Fläche A1. Die Fläche A1 berechnet sich aus der Flächenformel für einen Kreis.
Nehmen wir an, der Kolben hat einen Durchmesser von 10 mm dann berechnet sich die Fläche A1:
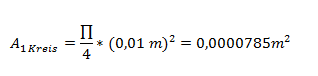
Mit den Einheiten aufpassen. Am besten immer in den Grundeinheiten Meter und Kilogramm rechnen!
Nun lässt sich auf den Druck im Zylinder schließen.

Zur Umrechnung einfach diesen Wert durch 100.000 teilen!
1 bar = 100.000 Pascal
Somit sprechen wir in diesem Fall von 12,5 bar Druck im Zylinder. Diesen Druck muss die Pumpe also mindestens aufbringen bzw. etwas mehr als das, um die Masse anzuheben.
Nehmen wir an, alles steht auf dem Kopf. Dann kommt die Fläche A2 zum Tragen.
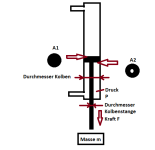

Die Fläche wird nun deutlich kleiner, weil man immer die Fläche der Kolbenstange abziehen muss! In diesem Fall hat die Kolbenstange einen Durchmesser von 5mm.
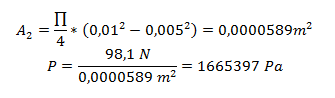
In diesem Fall also 16,65 bar! Diese Problematik zeigt auch, dass es schon einen erheblichen Unterschied macht, in welcher Einbaulage sich ein Hydraulikzylinder befindet!
Diese Berechnungen verdeutlichen ebenfalls den wichtigsten Satz der Hydraulik:
Der Druck in einem Hydrauliksystem hängt immer von der äußeren Last ab!!!
Nehmen wir an, es wird keine Masse angehoben, dann wirkt nur das Eigengewicht der Kolbenstange (wenige Gramm) als Masse mit der Schwerkraft. Die entstehende Kraft ist so gering, dass auch der Druck im System sehr gering ist. In diesem Fall muss die Hydraulikpumpe keine 12,5 bar oder 16,65 bar aufbringen, sondern nur ganz wenig Druck.
Ähnlich könnte das bei einem Radlader sein, die Schaufel ist nicht gefüllt, ihr hebt die Schaufel über die Fernsteuerung an, der Druck in eurem Hydrauliksystem entspricht dem Gewicht der Schaufel / Hubgerüst, wird also eher gering sein (wenige bar). Hebt ihr eine voll beladene Schaufel an, steigt der Druck im System erheblich. Um hier mal eine Größenordnung zu schaffen: Im Bereich der 1:14 / 1:16 Maßstäbe findet man Drücke zwischen 10 und 20 bar, aber auch das soll keine Pauschalaussage sein! Jeder Hersteller für Hydraulikpumpen gibt auch den Maximaldruck an.
3. Pumpen:
In den meisten Fällen kommen im Bereich der Hydraulikpumpen sogenannte Zahnradpumpen zum Einsatz. Zwei Zahnräder kämmen in einander und erzeugen einen Druck. Der erzeugte Druck in der Pumpe hängt natürlich wieder von der äußeren Last ab. Viel Last = großen Druck, wenig Last = kleiner Druck.
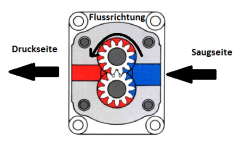
Das angesaugte Hydrauliköl fließt dabei außen entlang (nicht in der Mitte hindurch!). Angetrieben wird dabei immer nur ein Zahnrad, das andere wird ja automatisch mit angetrieben. Wenn ich das Zahnrad nun einmal drehe, verdrängt die Pumpe ein gewissen Volumen. Dieses Volumen nennt sich Schluckvolumen (Vg).
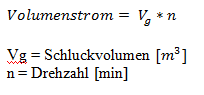
Der Volumenstrom ergibt sich also aus dem Schluckvolumen der Pumpe mal der Drehzahl pro Minute. Im Grunde genommen kann euch das egal sein, weil die Hersteller von Hydraulikpumpen den Volumenstrom angeben. Die ist insbesondere bei der Auslegung von hydraulischen Anlagen sehr wichtig. Möchte ich einen einzigen Zylinder (z.B. zum abkippen bei Lkw) oder mehrere (z.B. in einem Bagger) verwenden. Dieser Punkt kommt später.
Für alle die es interessiert: Das Schluckvolumen einer Zahnradpumpe berechnet sich aus dem Durchmesser eines Zahnrads. Man kann annäherungsweise folgendes annehmen:
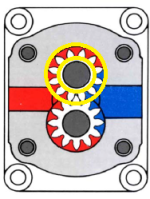
Die Fläche zwischen den beiden gelben Kreisen, multipliziert mit der Breite des Zahnrads, ergibt das Schluckvolumen. Innerhalb der Fläche zwischen den gelben Kreisen sind nur noch die Zahnflanken. Die Zwischenräume der Zahnflanken werden durch die Zahnflanken des zweiten Zahnrads gefüllt. Es ergibt sich die freie Fläche zwischen den beiden gelben Kreisen, diese noch multipliziert mit der Tiefe (Breite des Zahnrads) ergibt das Schluckvolumen bei einer Umdrehung.
Nehmen wir an, eine Pumpe ist direkt mit einem Hydraulikzylinder verbunden. Im Einschaltmoment fährt der Zylinder aus. Nach einer gewissen Zeit ist dieser am Anschlag angekommen und es geht nicht weiter. Was passiert mit dem Druck im System? Der Druck steigt theoretisch ins Unendliche. Die Pumpe versucht das Unmögliche, sie baut ihren Maximaldruck auf. Dieser ist durch die Antriebsleistung des Motors und durch die Dichtungen begrenzt. Ganz wichtig in diesem Zusammenhang ist somit IMMER DIE VERWENDUNG EINES DBV (Druckbegrenzungsventil). Alles andere führt dazu, dass die Pumpe beschädigt wird. Dichtungen gehen kaputt, Motoren werden sehr schnell heiß, weil diese ein hohes Drehmoment erzeugen müssen. Häufig ist das DBV auch schon fester Bestandteil einer gekauften Pumpe.
4. Druckbegrenzungsventil (DBV)
Das DBV begrenzt den Maximaldruck innerhalb eines hydraulischen Systems. Häufig ist das DBV auch schon fester Bestandteil einer gekauften Pumpe. Es ist meistens voreingestellt auf einen bestimmten Druck.
Nehmen wir an das DBV ist auf 10 bar eingestellt. Ihr wollt eine geringe Last anheben, es ergibt sich ein Druck im System von z.B. 9 bar. Kein Problem, ihr könnt die Last anheben, weil die Last im System unterhalb der 10 bar liegt. Jetzt verdoppelt ihr die Last, ihr braucht also auf einmal 18 bar Druck im System. Ihr könnt die Last nicht anheben, das DBV öffnet sobald der maximale Druck (in diesem Fall 10 bar) erreicht ist. Im Grund genommen schützt ihr damit eure Pumpe und das hydraulische System vor zu hohen Drücken. Wenn das DBV öffnet, fließt das Öl zurück in den Tank.
Dabei besteht ein DBV aus einer kleinen Metallkugel. Diese wird durch eine Feder vor ein Loch gedrückt und verschließt das Loch somit. Über eine Schraube lässt sich meistens die Vorspannung der Feder verstellen und damit die Kraft, die die Feder auf die Metallkugel ausübt.
Dazu bald mehr!
an dieser Stelle möchte ich versuchen ein paar grundsätzliche Fragen zum Thema der hydraulischen Anlagen zu klären und habe dazu mit der Erlaubnis von Winni (Admin) diesen FAQ-Bereich gegründet. Ich möchte dabei auch das Thema der Berechnungsgrundlagen erläutern. Ich werde die grundsätzlichen Funktionen von hydraulischen Anlagen erklären und auf die Komponenten eingehen. Ein paar Formeln sind zudem ebenfalls sinnvoll. Ich werde dabei teilweise in kleinen Schritten vorgehen, sodass es alle gut verstehen können. Viele von euch werden das meiste schon kennen, ich möchte insbesondere Einsteigern die Möglichkeit geben grundsätzliche Dinge zu verstehen.
Hintergrund: Ich selbst bin junger Maschinenbauingenieur und kenne mich in dem Bereich der Hydraulischen Systeme aus. Häufig liest man in Foren viel „Unfug“ und falsche Dinge. Grundsätzlich möchte ich das Thema allen etwas besser zugänglich machen. Ich hoffe es gefällt euch! Lob / Kritik sind gerne willkommen! Der Aufbau dieses FAQ-Bereichs wird etwas dauern.
1. Einleitung:
Hydraulische Anlagen erfreuen sich im Bereich des Modellbaus einer wachsenden Beliebtheit. Diese Anlagen bringen sehr viel Kraft auf und sind dabei meistens kompakter, kraftvoller und dynamischer als z.B. Spindelantriebe. Gleichzeitig aber auch komplexer und deutlich teurer.
Fangen wir an. Die wichtigste Formel im Bereich der Hydraulik ist folgende:
P=F/A (Druck ist gleich Kraft pro Fläche)
Ein Druck entsteht somit immer durch die Einwirkung einer Kraft auf eine Fläche.
P = Druck [Pascal oder bar]
F = Kraft [Newton]
A = Fläche [Quadratmeter]
Eine Kraft ergibt sich wie folgt
F=m*g (Kraft ist gleich Masse mal Beschleunigung)
F = Kraft [Newton]
m = Masse [Kilogramm]
g = Erdbeschleunigung (Konstante 9,81 m/s^2 )
2. Hydraulikzylinder
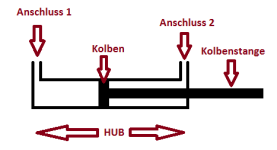
Die Abbildung zeigt einen doppelt wirkenden Hydraulikzylinder. Dieser kann in beide Richtungen (nach links und nach rechts) wirken. Es gibt auch Zylinder mit nur einem Anschluss z.B. bei einer Hebebühne für Pkw. Zum Anheben muss ich einen Druck aufbringen. Für das Absenken nehme ich den Druck wieder weg, den Rest erledigt die Schwerkraft.
In unserem Beispiel sind die wichtigsten geometrischen Daten der Kolbendurchmesser, der Kolbenstangendurchmesser und der Hub. Der Hub hat grundsätzlich nichts mit dem Druck zutun, aber dazu ein Beispiel:
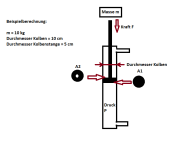
Nehmen wir an ihr wollt eine Masse von 10 kg anheben. Die Masse wirkt entgegen der Erdanziehungskraft. Es entsteht eine Kraft von:

Ihr müsst nun also eine Kraft von mehr als 98,1 aufbringen. Die Kraft wirkt über die Kolbenstange des Zylinders auf die Fläche A1. Die Fläche A1 berechnet sich aus der Flächenformel für einen Kreis.
Nehmen wir an, der Kolben hat einen Durchmesser von 10 mm dann berechnet sich die Fläche A1:
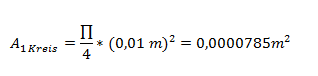
Mit den Einheiten aufpassen. Am besten immer in den Grundeinheiten Meter und Kilogramm rechnen!
Nun lässt sich auf den Druck im Zylinder schließen.

Zur Umrechnung einfach diesen Wert durch 100.000 teilen!
1 bar = 100.000 Pascal
Somit sprechen wir in diesem Fall von 12,5 bar Druck im Zylinder. Diesen Druck muss die Pumpe also mindestens aufbringen bzw. etwas mehr als das, um die Masse anzuheben.
Nehmen wir an, alles steht auf dem Kopf. Dann kommt die Fläche A2 zum Tragen.
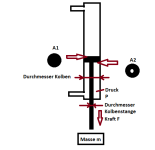

Die Fläche wird nun deutlich kleiner, weil man immer die Fläche der Kolbenstange abziehen muss! In diesem Fall hat die Kolbenstange einen Durchmesser von 5mm.
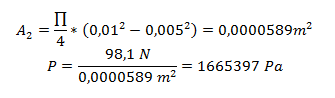
In diesem Fall also 16,65 bar! Diese Problematik zeigt auch, dass es schon einen erheblichen Unterschied macht, in welcher Einbaulage sich ein Hydraulikzylinder befindet!
Diese Berechnungen verdeutlichen ebenfalls den wichtigsten Satz der Hydraulik:
Der Druck in einem Hydrauliksystem hängt immer von der äußeren Last ab!!!
Nehmen wir an, es wird keine Masse angehoben, dann wirkt nur das Eigengewicht der Kolbenstange (wenige Gramm) als Masse mit der Schwerkraft. Die entstehende Kraft ist so gering, dass auch der Druck im System sehr gering ist. In diesem Fall muss die Hydraulikpumpe keine 12,5 bar oder 16,65 bar aufbringen, sondern nur ganz wenig Druck.
Ähnlich könnte das bei einem Radlader sein, die Schaufel ist nicht gefüllt, ihr hebt die Schaufel über die Fernsteuerung an, der Druck in eurem Hydrauliksystem entspricht dem Gewicht der Schaufel / Hubgerüst, wird also eher gering sein (wenige bar). Hebt ihr eine voll beladene Schaufel an, steigt der Druck im System erheblich. Um hier mal eine Größenordnung zu schaffen: Im Bereich der 1:14 / 1:16 Maßstäbe findet man Drücke zwischen 10 und 20 bar, aber auch das soll keine Pauschalaussage sein! Jeder Hersteller für Hydraulikpumpen gibt auch den Maximaldruck an.
3. Pumpen:
In den meisten Fällen kommen im Bereich der Hydraulikpumpen sogenannte Zahnradpumpen zum Einsatz. Zwei Zahnräder kämmen in einander und erzeugen einen Druck. Der erzeugte Druck in der Pumpe hängt natürlich wieder von der äußeren Last ab. Viel Last = großen Druck, wenig Last = kleiner Druck.
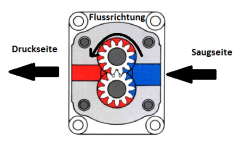
Das angesaugte Hydrauliköl fließt dabei außen entlang (nicht in der Mitte hindurch!). Angetrieben wird dabei immer nur ein Zahnrad, das andere wird ja automatisch mit angetrieben. Wenn ich das Zahnrad nun einmal drehe, verdrängt die Pumpe ein gewissen Volumen. Dieses Volumen nennt sich Schluckvolumen (Vg).
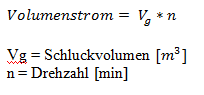
Der Volumenstrom ergibt sich also aus dem Schluckvolumen der Pumpe mal der Drehzahl pro Minute. Im Grunde genommen kann euch das egal sein, weil die Hersteller von Hydraulikpumpen den Volumenstrom angeben. Die ist insbesondere bei der Auslegung von hydraulischen Anlagen sehr wichtig. Möchte ich einen einzigen Zylinder (z.B. zum abkippen bei Lkw) oder mehrere (z.B. in einem Bagger) verwenden. Dieser Punkt kommt später.
Für alle die es interessiert: Das Schluckvolumen einer Zahnradpumpe berechnet sich aus dem Durchmesser eines Zahnrads. Man kann annäherungsweise folgendes annehmen:
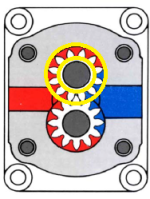
Die Fläche zwischen den beiden gelben Kreisen, multipliziert mit der Breite des Zahnrads, ergibt das Schluckvolumen. Innerhalb der Fläche zwischen den gelben Kreisen sind nur noch die Zahnflanken. Die Zwischenräume der Zahnflanken werden durch die Zahnflanken des zweiten Zahnrads gefüllt. Es ergibt sich die freie Fläche zwischen den beiden gelben Kreisen, diese noch multipliziert mit der Tiefe (Breite des Zahnrads) ergibt das Schluckvolumen bei einer Umdrehung.
Nehmen wir an, eine Pumpe ist direkt mit einem Hydraulikzylinder verbunden. Im Einschaltmoment fährt der Zylinder aus. Nach einer gewissen Zeit ist dieser am Anschlag angekommen und es geht nicht weiter. Was passiert mit dem Druck im System? Der Druck steigt theoretisch ins Unendliche. Die Pumpe versucht das Unmögliche, sie baut ihren Maximaldruck auf. Dieser ist durch die Antriebsleistung des Motors und durch die Dichtungen begrenzt. Ganz wichtig in diesem Zusammenhang ist somit IMMER DIE VERWENDUNG EINES DBV (Druckbegrenzungsventil). Alles andere führt dazu, dass die Pumpe beschädigt wird. Dichtungen gehen kaputt, Motoren werden sehr schnell heiß, weil diese ein hohes Drehmoment erzeugen müssen. Häufig ist das DBV auch schon fester Bestandteil einer gekauften Pumpe.
4. Druckbegrenzungsventil (DBV)
Das DBV begrenzt den Maximaldruck innerhalb eines hydraulischen Systems. Häufig ist das DBV auch schon fester Bestandteil einer gekauften Pumpe. Es ist meistens voreingestellt auf einen bestimmten Druck.
Nehmen wir an das DBV ist auf 10 bar eingestellt. Ihr wollt eine geringe Last anheben, es ergibt sich ein Druck im System von z.B. 9 bar. Kein Problem, ihr könnt die Last anheben, weil die Last im System unterhalb der 10 bar liegt. Jetzt verdoppelt ihr die Last, ihr braucht also auf einmal 18 bar Druck im System. Ihr könnt die Last nicht anheben, das DBV öffnet sobald der maximale Druck (in diesem Fall 10 bar) erreicht ist. Im Grund genommen schützt ihr damit eure Pumpe und das hydraulische System vor zu hohen Drücken. Wenn das DBV öffnet, fließt das Öl zurück in den Tank.
Dabei besteht ein DBV aus einer kleinen Metallkugel. Diese wird durch eine Feder vor ein Loch gedrückt und verschließt das Loch somit. Über eine Schraube lässt sich meistens die Vorspannung der Feder verstellen und damit die Kraft, die die Feder auf die Metallkugel ausübt.
Dazu bald mehr!
